隨著社會的不斷發(fā)展和進步,越來越多的企業(yè)開始用PLM武裝自己。PLM不僅僅是一類軟件的統(tǒng)稱,更重要的是,PLM作為一種企業(yè)戰(zhàn)略可用來搭建標準環(huán)境來管理和跟蹤產(chǎn)品的全生命周期數(shù)據(jù)。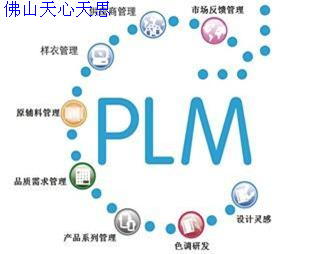
PLM將產(chǎn)品研發(fā)、制造和服務部門緊密地結(jié)合起來,企業(yè)可以此為平臺管理并完善有效的運作流程。在企業(yè)PLM框架內(nèi)將不同的軟件及流程集成起來是一個復雜的系統(tǒng)工程,我們必須考慮如何將產(chǎn)品周期不同階段(包括設計、工藝、制造及維護等)的各類數(shù)據(jù)和信息進行有效地鏈結(jié)及重復利用。
企業(yè)成功實施PLM戰(zhàn)略需要在時間和金錢上作巨大投入,這還包括企業(yè)對自身流程的深刻認識和理解。為了配合企業(yè)對投資匯報率(ROI)孜孜不倦的追求,許多PLM供應商建議企業(yè)分塊實施PLM,以期取得更快的投資回報。在這種趨勢下,以PLM為框架實施MES能為企業(yè)帶來巨大的經(jīng)濟效益。
制造執(zhí)行系統(tǒng)(MES)是企業(yè)整個PLM (產(chǎn)品全生命周期管理) 戰(zhàn)略的重要一環(huán)。在生產(chǎn)過程中,原材料、工人、設備、工藝、產(chǎn)品設計及企業(yè)最佳實踐知識在最大程度上融合在一起,而MES管理著所有的車間級生產(chǎn)活動的實時記錄和數(shù)據(jù)。換句話說,在PLM框架內(nèi),MES的主要功能是記錄、存儲及共享實時的用以描述產(chǎn)品加工過程的信息,例如工時和原材料的消耗,產(chǎn)品追蹤及裝配關(guān)系,加工過程偏差等等。只有通過MES,我們才能知道已生產(chǎn)出哪些產(chǎn)品,這些產(chǎn)品的生產(chǎn)過程,以及這些產(chǎn)品是否按照規(guī)格和計劃生產(chǎn)出來,如有偏差,偏差有多大。正在實施六西格瑪質(zhì)量方案的企業(yè),以此為途徑,將能顯著地降低產(chǎn)品及制造過程偏差。
企業(yè)逐漸意識到將產(chǎn)品設計,工藝規(guī)劃與生產(chǎn)現(xiàn)場進行關(guān)聯(lián)的重要性,比如在制造航空發(fā)動機的過程中,PLM的前期階段即產(chǎn)品設計和工藝規(guī)劃已明確制訂各制造步驟,并據(jù)此生成工作指導書下達到車間執(zhí)行,車間操作人員必須嚴格依據(jù)工作指導書,將正確的零部件,按正確的配置,依照正確加工和裝配次序,生產(chǎn)出正確的產(chǎn)品;同時,掌握生產(chǎn)現(xiàn)場狀況對於企業(yè)來說是非常關(guān)鍵的,我們需要隨時了解各訂單的生產(chǎn)狀況,包括零部件庫存、在制品、人工及材料消耗等指標,并把這些數(shù)據(jù)存入PLM數(shù)據(jù)庫,以提供給企業(yè)其它協(xié)同部門。
盡管MES的實施技術(shù)和方法正在發(fā)生轉(zhuǎn)變,當前MES仍著眼于從設備自動化的角度去提高生產(chǎn)效率并解決生產(chǎn)線上的瓶頸問題。這種策略往往忽視了建立實時生產(chǎn)記錄的重要性-在運行設備上及操作過程中采集的實時數(shù)據(jù),如果通過有效的管道提供給相關(guān)的設計及工藝部門,可以幫助企業(yè)判別真正的生產(chǎn)過程與產(chǎn)品、工藝方案間的偏差,以利於企業(yè)提高各類企業(yè)資源的利用率并促進產(chǎn)品的更新?lián)Q代。
企業(yè)在從PLM角度去實施MES的時候,需要考慮在系統(tǒng)集成、變更管理及流程管理中如何充分利用MES采集的實時生產(chǎn)數(shù)據(jù)。
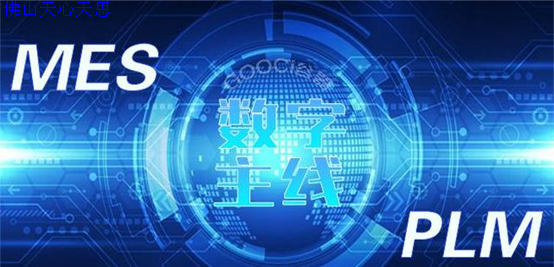
在集成的環(huán)境下,MES用戶可通過網(wǎng)絡瀏覽器訪問源自PLM、ERP和SCM的數(shù)據(jù)。產(chǎn)品和工藝數(shù)據(jù)、零部件物理模型、工作指導書,以及相關(guān)的供應商信息既可作為車間生產(chǎn)的依據(jù),還可作為支持生產(chǎn)現(xiàn)場管理的重要手段。通過將在PLM中定義的產(chǎn)品及規(guī)劃數(shù)據(jù)與實時的生產(chǎn)數(shù)據(jù)(例如過程偏差,廢品率及返工率)相對比,用戶將能夠及時調(diào)整加工過程,也能為后續(xù)的工藝過程優(yōu)化埋下伏筆。企業(yè)不同部門,甚至不同機構(gòu)(OEM/供應商)均應能訪問此類數(shù)據(jù),以發(fā)揮數(shù)據(jù)共享的最高效率。
在生產(chǎn)過程中,原材料、工人、設備、工藝、產(chǎn)品設計及企業(yè)最佳實踐知識在最大程度上融合在一起,源自產(chǎn)品周期不同階段(包括設計、工藝、制造及維護等)的各類數(shù)據(jù)和信息在此階段得到有效的鏈結(jié)及重復利用。所以企業(yè)信息化是一項集成技術(shù),企業(yè)建設信息化的關(guān)鍵點在于信息的集成和共享。